What Kind of Connection Methods for Steel Wire Ropes?
- Share
- Issue Time
- Oct 21,2021
Summary
The wire rope needs to be connected with other load-bearing parts to transfer the load. This article will specifically introduce the connection methods of the steel wire rope.
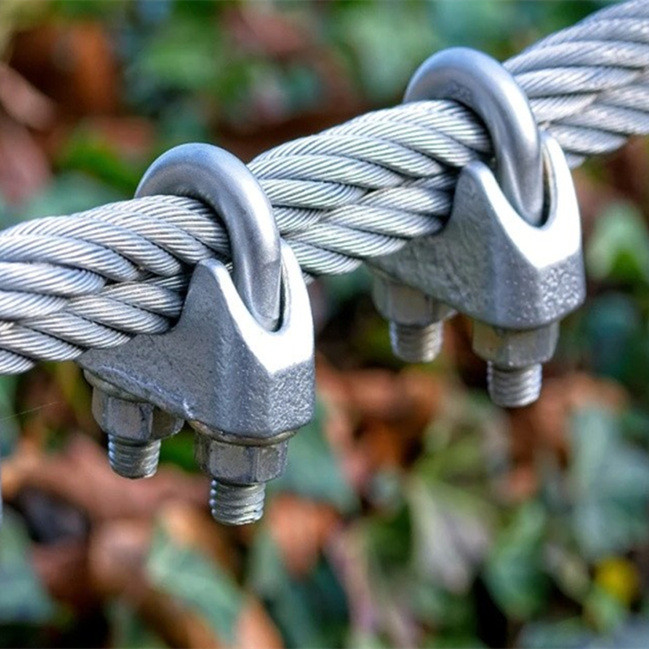
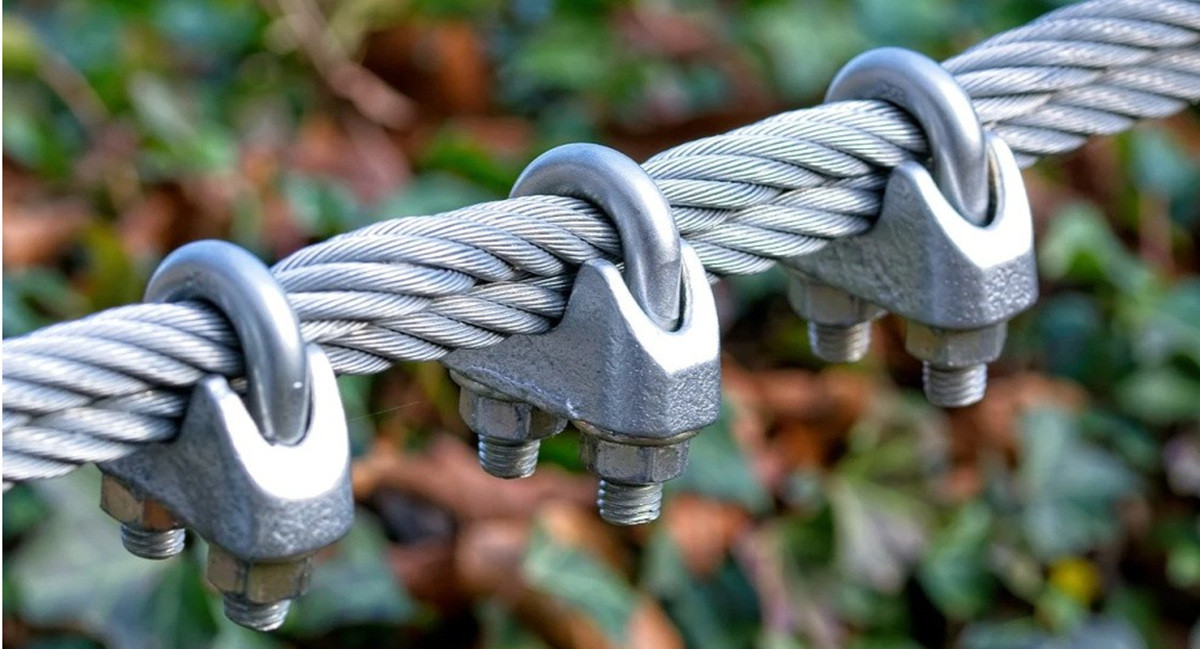
The wire rope needs to be connected with other load-bearing parts to transfer the load. Different connection methods require attention and application scenarios are different, and the connection methods are rough as follows.
1. Weaving method
The wire rope joint adopts the plug-in method, and the plug-in length shall not be less than 20 times the diameter, and the total length shall not be shorter than 300mm.
(1) The manual inserting operation should be interspersed for each strand at least five times, and the whole strand should be interspersed for at least three of the five times. For a smooth transition of plug-in joints, you can use the strands with part of the steel wire cut off for the last or second insertion. (On site, three whole strands are interspersed, 6 strands totaling 18 stitches)
(2) The mechanical insertion operation consists of three strands interspersed four times, and the other three strands interspersed five times. (Interleaved 27 times)
(3) Weld the ends of each wire rope.
(4) The rope core of the inserting part must not be exposed, and the strands must be tight and not loose.
(5) The cut ends of the rope strands after weaving should be straight, and there should be no obvious distortion.
2. Soka connection
The method of using the Soka connection is suitable for non-lifting steel wire rope connection to my head. (This method is used for hoisting oil roof wire rope on site)
(1) When fixing with rope clamps, pay attention to the number of rope clamps, the distance between the rope clamps, the direction of the rope clamps, and the strength of the fixing place.
(2) The fastening of the clamping method must be checked frequently, and the connection strength is not less than 85% of the breaking force of the wire rope.
(3) The rope clamp pressure plate should be on the side of the long end of the wire rope. The rule of thumb is that the distance between the rope clamps is not less than 6 times the diameter of the wire rope.
3. Sleeve method
Using reliable technology to make the aluminum alloy sleeve and the steel wire rope fit tightly and firmly, the connection strength should reach the breaking force of the steel wire rope.
(1) The standard stipulates that the pressing sleeve material is 3A211112 (this material can only be used on product rigging) or 5A02H112 aluminum and aluminum alloy extruded seamless round pipes.
(2) The surface of the flat oval tube should be smooth, free of burrs, cracks, mechanical damage, and other obvious defects.
(3) Use ultrasonic flaw detection to check the internal defects of the pipe, and no shrinkage, cracks, delamination, slag inclusion, etc. are allowed.
(4) The size of the round pipe should be matched with the diameter of the wire rope, and it should be confirmed by checking the table. (The diameter of the wire rope used in the field is 24mm, the length of the oval flat tube is about 101mm, and the thickness is about 11.2mm)
(5) The joint is not allowed to be bent during use, and the operating temperature is -40°C~+150°C.
(6) The moving distance L between the joint and the rope sleeve must be 3 times the hook width B or 15 times the wire rope diameter.
(7) The end of the steel wire rope shall not be loose before pressurization. The joint should be able to withstand a static load of 90% of the minimum breaking force of the wire rope and an impact load of 15%~30% of the minimum breaking force.
(8) The center distance between the two sets of rings shall not be less than 40 times the diameter of the wire rope.
4. The method of oblique wedge fixation
The wedge and the wedge sleeve are connected so that one end of the wire rope goes around the wedge, and the wire rope is fixed by the locking effect of the wedge in the sleeve. The strength of the anchorage is about 75%~85% of the strength of the rope itself. The wedge sleeve should be made of steel, and the connection strength should not be less than 75% of the breaking force of the wire rope.
The wedge taper method is usually only used to fix steel wire ropes with a diameter below 40mm.
5. Lead filling method
The lead filling method of the cone sleeve is referred to as the lead filling method. After the core is inserted into the cone sleeve, the end of the wire rope is bent into a hook shape, and then the molten lead liquid is poured into it, and it is finished after cooling. This method is complicated to operate, and it is rarely used today.
When the tapered wedge is connected, its connection strength should reach the breaking force of the wire rope.
6. The method of pressing plate consolidation
Press plate consolidation method This method is mainly used to fix the end of the wire rope on the lifting or luffing drum. The bottom surface of the press plate is equipped with a rope groove to compress the wire rope. During construction, first, make the end of the wire rope pass through the end plate of the reel, then bend it together, and then clamp it with a grooved pressure plate, and finally secure the pressure plate on the end plate of the reel with bolts.
The connection of the wire rope is related to the safety and stability of the application, so it is very important to choose the appropriate connection method. If you want to know more about wire rope after reading the above, you can get a comprehensive solution by contacting us.
With excellent production technology and considerate service, we quickly become one of the leading hardware manufacturers. We have strict requirements on product quality and craftsmanship, carry out comprehensive inspection and management, and have received good feedback from many customers. We also provide customers with a variety of options and provide thoughtful one-stop service according to customer needs. If you want to buy our wire rope, please contact us immediately!